American Plastic Molds are special tools used to produce plastic products. They are made from different types of plastic materials and can have multiple cavities or inserts.
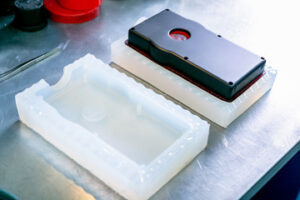
They are best suited for short runs of plastic parts that require little to no revisions. They can also save time and money by reducing the number of production cycles needed to complete a project.
The plastic injection moulding process is one of the most common ways that components can be made from a specific polymer. This method is able to deliver stunning levels of accuracy and a high quality finish for components that are complex in design. Injection moulding is also an extremely efficient way to manufacture parts and can often be completed in a shorter amount of time than some other methods.
The first step is to prepare the material for molding. The plastic is granulated and then heated so that it can be melted into liquid form. This can be done using either hot oil or a chemical solution depending on the specific product being manufactured. Once the granules are melted they are then fed into the injection machine through a screw. This is a barrel-shaped screw that has been optimized for the injection molding process, ensuring the correct pressure is built up and that the melted plastic is injected quickly into the mold cavity.
Once the molten plastic is inserted into the mold cavity it begins to cool down and solidify. This is a critical part of the injection molding process as it allows the molded part to take shape and takes its final appearance. Once the plastic is cooled it can then be removed from the mold and is ready for use.
Injection molding is a highly repeatable process, which allows for the production of a high volume of parts with a very high standard of quality. It is also an environmentally friendly process, as any waste plastic can be reground and fed back into the injection machine for use in the manufacturing process.
However, the process does have its drawbacks, such as a high initial cost for set-up of machinery and production. It is also a slower process than some other high-speed processes and it requires skilled workers to operate.
Another issue is the formation of ‘knit lines’, which are small hair-like discolorations that can occur when different flows of melted plastic meet. This is usually due to an abrupt geometry change in a part. This can be avoided by designing parts with smooth changes in wall thickness and by adding ribs where possible.
Extrusion Moulding
Extrusion moulding involves the process of forming long lengths of thermoplastic material. It is a good method for producing pipes, curtain rails, and other products that require long, continuous shapes. The plastic is formed in a die that has been custom-designed to the desired shape and profile of the product. The molten plastic is then cooled to solidify it into the final product. Extrusion moulding is a more cost-efficient method of producing plastic products than injection molding. It is also more environmentally friendly since it produces less waste.
Injection molding requires a significant amount of energy to melt and shape the plastic. This process generates a lot of waste in the form of sprues and runners, which are channels through which the melted plastic travels before entering the mold cavity. This waste is often ground up and recycled, which reduces both production costs and environmental impact. Extrusion, on the other hand, uses a minimal amount of energy to create the final product. This makes it an ideal method for manufacturing larger quantities of products.
Plastic extrusion is a complex and time-consuming process, but it offers a number of benefits that make it a better choice than other methods for creating plastic products. For example, it can be used to manufacture a wide range of shapes and sizes, and it can produce high volumes in a short period of time. Additionally, it can be used to produce hollow and semi-hollow products, such as tubes and rods.
When designing a new plastic extruded product, manufacturers must consider several factors, including draft angles, wall thickness, and the diameter of the profile. For example, draft angles help to control air flow and prevent blowouts in the finished product. Wall thickness is important because it influences how quickly the molded product will cool. A too-thick wall will result in a longer cooling time and could lead to quality issues.
To maximize the efficiency of the plastic extrusion process, manufacturers should optimize their equipment to ensure that it is delivering the best results. This can include balancing the material flow, adjusting the temperature, and minimizing the pressure. Manufacturers should also be careful to avoid making mistakes that could cause problems with the overall process. This is especially true in the initial stages of the design process.
Rotomoulding
The rotomoulding process is one of the most versatile in plastic manufacturing. It can produce large, seamless products with a high degree of uniformity in their wall thickness. It is also able to create complex shapes that cannot be created through other processes like injection molding. In addition, rotomoulding allows for flexible production and is often cost-effective.
In the rotomoulding process, powdered resin is heated inside a hollow mold and slowly rotates on two perpendicular axes. The rotation of the mold and the slow heating help to distribute the resin evenly. The resulting molten plastic then fills the shape of the mold and solidifies. After the product is fully molded, it is cooled by air or water and then removed from the mould.
When choosing a rotomolding machine, it is important to consider its capacity and the materials it will be using. It is also important to understand how the rotomolding process works and the safety measures involved in it. This will ensure that the machine can be used safely and effectively. It is recommended to have experienced technicians carry out regular inspections of the machine to assess its performance and safety standards.
In rotomoulding, the mold must be made of materials that can withstand the high temperatures during the heating and cooling cycles. It is also a good idea to incorporate a draft angle into the design of the product, which will make it easier for operators to remove the finished product from the mold without damaging it.
It is also essential to ensure that the proper rotation ratio is used for the rotomolded part. For spherical or cubic shapes, a ratio of 4:1 is usually sufficient. However, if the product has an irregular shape, it may be necessary to use a higher ratio in order to ensure even distribution of the wall thickness.
Lastly, it is important to note that the rotomolded product must be cooled quickly and at a controlled rate. This is because if it cools too rapidly, it will shrink and warp. This can be prevented by using a fan to cool the mold and by keeping the rotation rate within a certain range.
Thermoforming
Thermoforming is a plastic forming method that uses heat to change the shape of thermoplastic materials. This process is used to create complex shapes that would be difficult or impossible to produce using other forming methods. Thermoforming is commonly used in the automotive, aerospace, and electronics industries.
During the thermoforming process, a plastic sheet is heated until it softens, then stretched over or into a mold. The plastic is then formed using vacuum, air pressure, or mechanical force to conform to the shape of the mold. Once the plastic has been formed, it is allowed to cool before being trimmed and inspected.
The thermoforming process can be used to make parts with a variety of textures and finishes. This makes it a versatile choice for products that require both aesthetic and functional properties, such as automotive components and medical devices. Thermoforming can also be used to create parts that fit together seamlessly, which reduces assembly time and improves the quality of the finished product.
To start the thermoforming process, a mold must be designed. There are two major types of molds used for thermoforming: positive and negative. Positive molds have a contour that defines the outer surface of the final part, while negative molds have a concave shape that forms the inner surface of the finished part. Once the mold is designed, it is constructed from aluminum or another material and is then used to form the plastic.
Depending on the type of plastic and the mold, there are various forming processes that can be used. Vacuum forming is the most common, in which the plastic sheet is heated until it becomes soft and then placed over a 3D mold. Air pressure is then applied to the sheet to remove any air between the mold and the plastic, which forces the sheet into place. The mold is then closed and the plastic is allowed to harden.
Thermoforming is a cost-effective manufacturing process that can be used to produce large plastic creations. Thermoformed parts are often lighter than their metal counterparts and offer improved impact resistance, making them a popular choice for many different applications. For example, thermoformed parts are often used in filtration and water systems to ensure high quality, durable results. They can also be found in recreational ATVs and construction and farm equipment, where they are needed to provide sturdy, long-lasting protection.